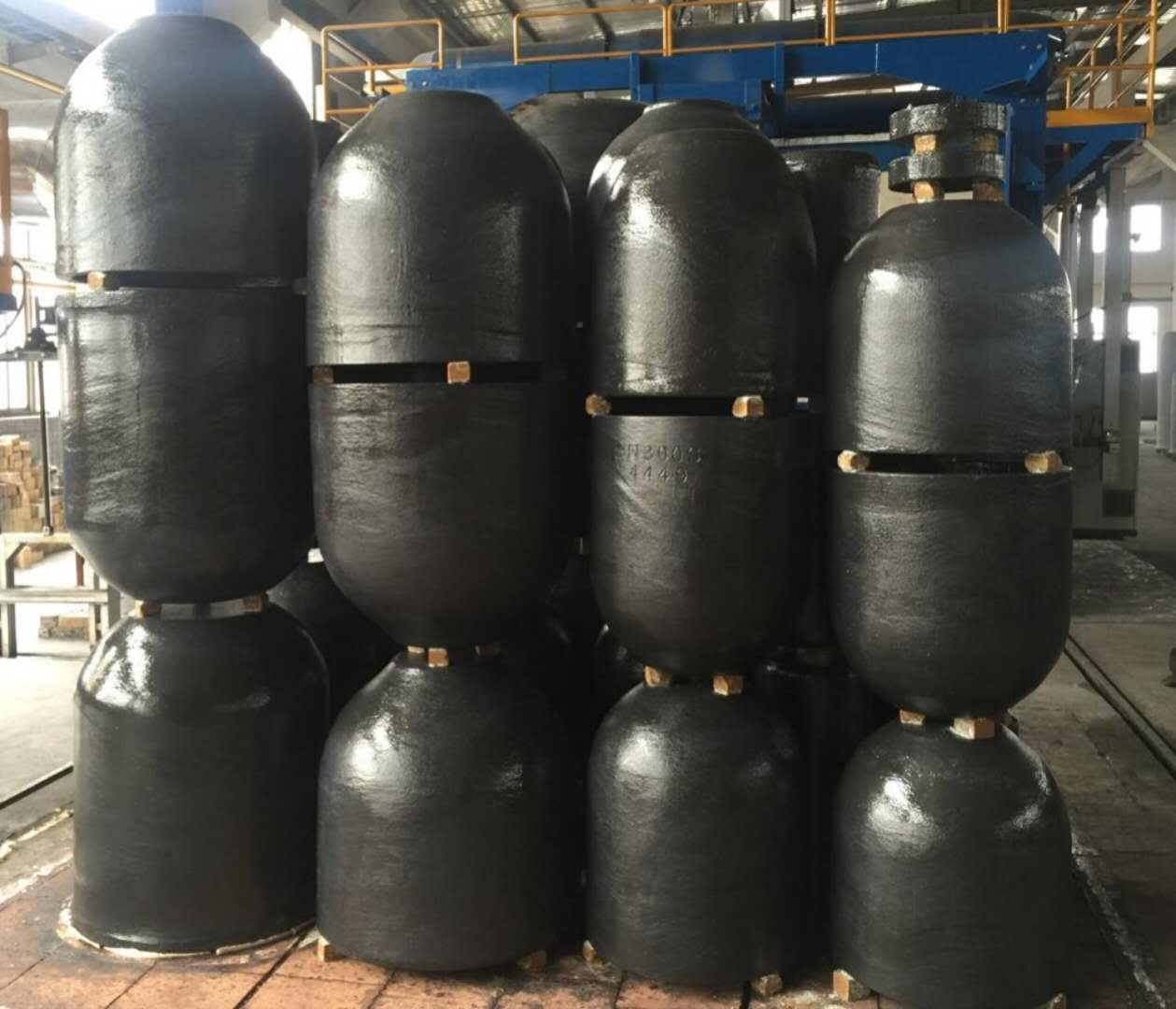
Aperçu
Le Crucible en graphiteest fabriqué à partir de graphite de flocons naturels comme principale matière première et est traité avec de l'argile ou du carbone réfractaire en plastique comme liant. Il a les caractéristiques d'une résistance à haute température, d'une forte conductivité thermique, d'une bonne résistance à la corrosion et d'une longue durée de vie. Lors d'une utilisation à haute température, le coefficient d'expansion thermique est faible et il a certaines performances de résistance à la déformation pour le refroidissement rapide et le chauffage. Il a une forte résistance à la corrosion aux solutions acides et alcalines, une excellente stabilité chimique et ne participe pas à des réactions chimiques pendant le processus de fusion. La paroi intérieure du creuset en graphite est lisse, et le liquide métallique fondu n'est pas facile à fuir et à adhérer à la paroi intérieure du creuset, ce qui fait que le liquide métallique a une bonne fluidité et une capacité de coulée, adapté à la coulée et à la formation de différents moules. En raison des excellentes caractéristiques ci-dessus, les creusets en graphite sont largement utilisés dans la fusion de l'acier à outils en alliage et des métaux non ferreux et leurs alliages.
Taper
Les creusets en graphite sont principalement utilisés pour la fusion des matériaux métalliques, qui sont divisés en deux types: le graphite naturel et le graphite artificiel.
1) Graphite naturel
Il est principalement en graphite de flocons naturels comme principale matière première, avec l'ajout d'argile et d'autres matières premières réfractaires. Il est généralement appelé creuset en graphite en argile, tandis qu'un creuset de type de liant en carbone est fabriqué avec de l'asphalte comme liant. Il est fait uniquement par la force de frittage de l'argile et est appelé creuset de type de type de liant d'argile Hui. Le premier a une résistance supérieure et une résistance aux chocs thermiques. Il est utilisé pour la fusion des alliages d'acier, de cuivre, de cuivre et d'autres métaux non ferreux, avec différentes tailles et capacités de fusion allant de 250 g à 500 kg.
Ce type de creuset comprend des accessoires tels qu'une cuillère écréphabituelle, un couvercle, une bague joint, un support de creuset et une tige d'agitation.
2) Graphite artificiel
Les creusets en graphite naturel mentionnés ci-dessus contiennent généralement environ 50% de minéraux argileux, tandis que les impuretés (teneur en cendres) dans les creusets en graphite artificiel sont inférieurs à 1%, utilisés pour affiner les métaux de haute pureté. Il existe également du graphite de haute pureté qui a subi un traitement de purification spécial (teneur en cendres <20 ppm). Les creusets en graphite artificiel sont souvent utilisés pour faire fondre de petites quantités de métaux précieux, de métaux de haute pureté ou de métaux et d'oxydes de point de fusion élevés. Il peut également être utilisé comme creuset pour l'analyse des gaz en acier.
Processus de production
Le processus de fabrication des creusets en graphite peut être divisé en trois types: moulure manuelle, moulure en rotation et moulure de compression. La qualité du creuset est étroitement liée à la méthode de moulage de processus. La méthode de formation détermine la structure, la densité, la porosité et la résistance mécanique du corps du creuset.
Des creusets moulés à la main à des fins spéciales ne peuvent pas être formés à l'aide de méthodes de moulage rotatif ou de compression. Certaines creusettes de forme spéciale peuvent être formées en combinant le moulage rotatif et le moulage à main.
Le moulage rotatif est un processus dans lequel une machine rotative peut conduire le moule au fonctionnement et utilise un couteau interne pour extruder de l'argile pour compléter le moulage du creuset.
Le moulage par compression est l'utilisation d'équipements de pression tels que la pression d'huile, la pression de l'eau ou la pression de l'air comme énergie cinétique, en utilisant des moules en acier comme outils plastiques pour la formation de creuset. Par rapport à la méthode du moulage rotatif, il présente les avantages d'un processus simple, d'un cycle de production court, d'un rendement élevé et d'efficacité, d'une faible intensité de main-d'œuvre, d'une humidité à faible moulage, d'un rétrécissement et de la porosité à faible creuset, à une qualité et une densité de produit élevée.
Soins et préservation
Les creusets en graphite doivent être protégés de l'humidité. Les creusets en graphite ont le plus peur de l'humidité, ce qui peut avoir un impact significatif sur la qualité. S'il est utilisé avec un creuset humide, il peut provoquer la fissuration, l'éclatement, la baisse du bord et la chute du fond, entraînant une perte de métal fondu et même des accidents liés au travail. Par conséquent, lors du stockage et de l'utilisation de creusets en graphite, l'attention doit être accordée à la prévention de l'humidité.
L'entrepôt pour stocker des creusets en graphite doit être sec et ventilé, et la température doit être maintenue entre 5 ℃ et 25 ℃, avec une humidité relative de 50 à 60%. Les creusets ne doivent pas être stockés sur un sol en briques ou un sol de ciment pour éviter l'humidité. Le creuset en graphite en vrac doit être placé sur un cadre en bois, de préférence à 25 à 30 cm au-dessus du sol; Emballés dans des boîtes en bois, des paniers en osier ou des sacs de paille, les dormeurs doivent être placés sous les palettes, pas moins de 20 cm au-dessus du sol. Placer une couche de feutre sur les traverses est plus propice à l'isolation d'humidité. Pendant une certaine période d'empilement, il est nécessaire d'empiler la couche inférieure à l'envers, de préférence avec les couches supérieures et inférieures face à face. L'intervalle entre l'empilement et l'empilement ne doit pas être trop long. Généralement, l'empilement doit être effectué une fois tous les deux mois. Si l'humidité du sol n'est pas élevée, l'empilement peut être fait une fois tous les trois mois. En bref, l'empilement fréquent peut obtenir un bon effet résistant à l'humidité.
Heure du poste: sept-13-2023