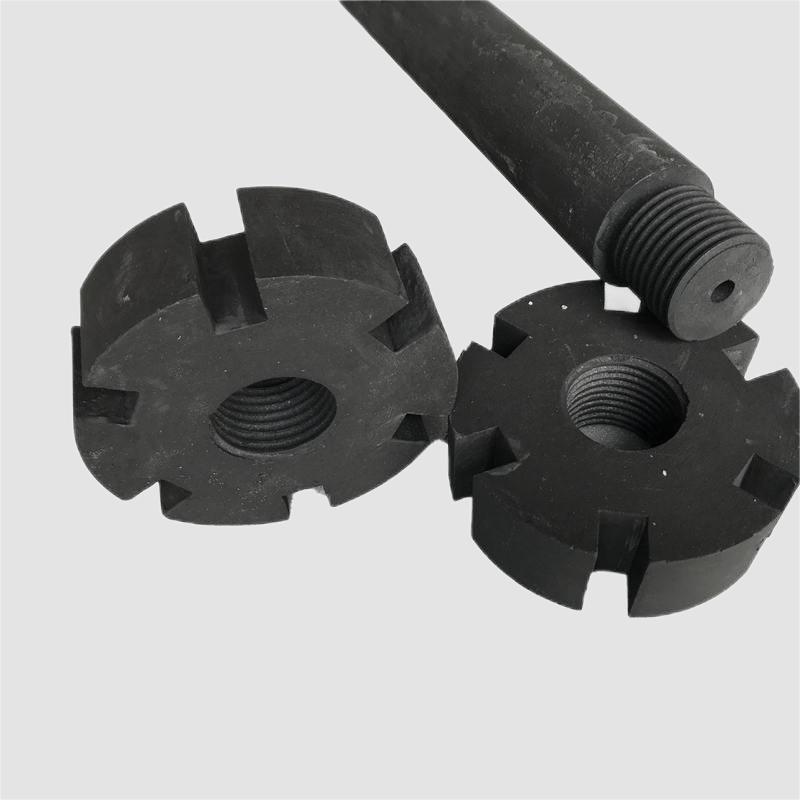
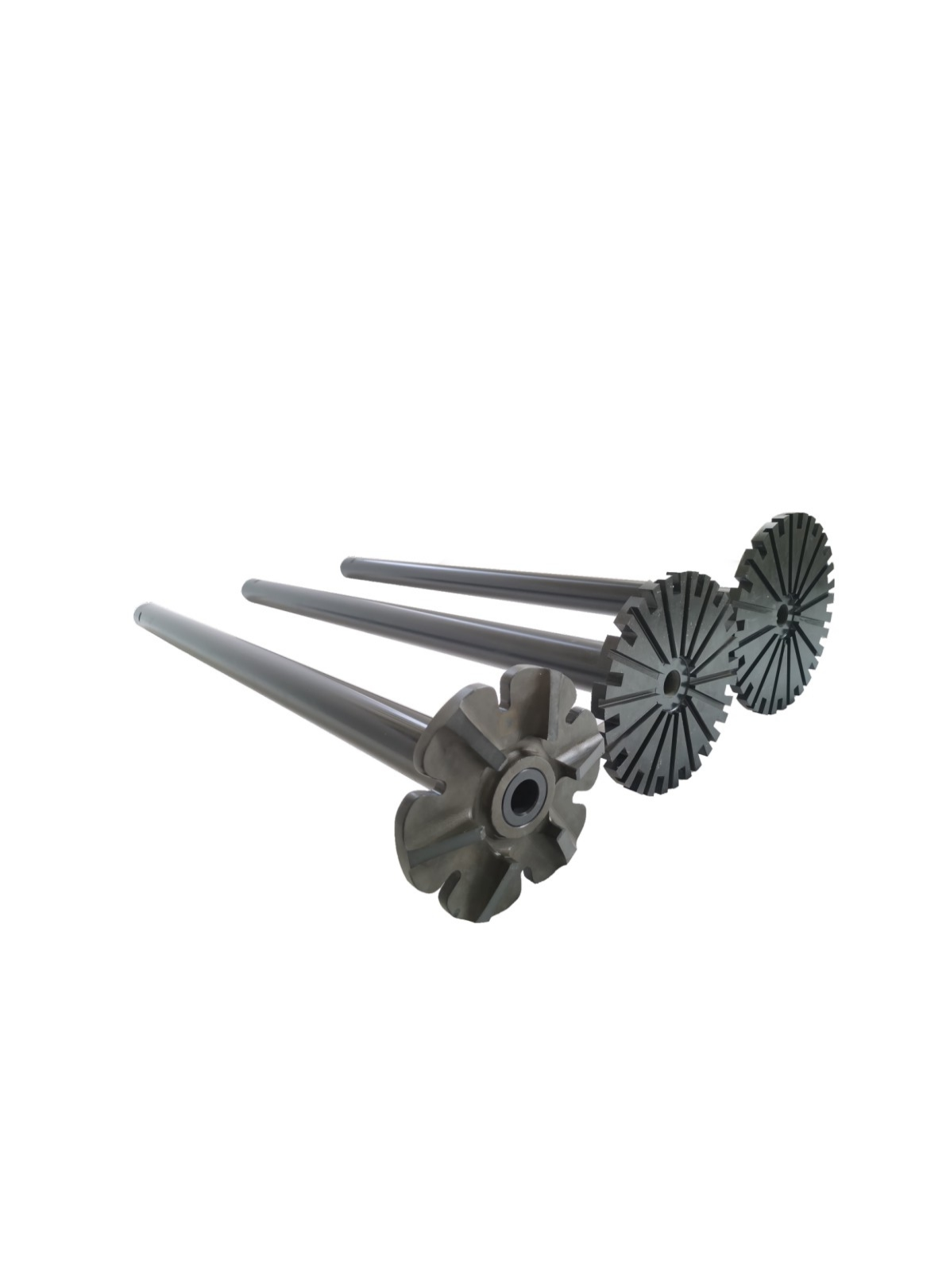
Introduction du produit:
Le principe de travail d'unrotor de graphiteest que le rotor rotatif brise l'azote (ou l'argon) soufflé dans la fonte en aluminium en un grand nombre de bulles dispersées et les disperse dans le métal fondu. Les bulles dans la fusion absorbent l'hydrogène de la fusion en fonction du principe de la différence de pression partielle du gaz et de l'adsorption de surface, des scories d'oxydation adsorb et sont effectuées de la surface de la fusion à mesure que les bulles se lèvent, permettant à la fusion d'être purifiée. En raison de la fine dispersion des bulles, ils se mélangent uniformément avec la fonte rotative et flottent lentement en spirale. Ils ont un long temps de contact avec la fusion et ne forment pas un flux d'air continu vers le haut, éliminant ainsi l'hydrogène nocif de la fonte d'aluminium et améliorant considérablement l'effet de purification.
Caractéristiques des produits de rotor graphite:
1. La buse rotative du rotor de graphite est en graphite de haute pureté. 2. Après le traitement de la surface, la durée de vie est environ trois fois celle des produits ordinaires, et il est largement utilisé dans l'industrie de la coulée en alliage en aluminium.
En termes d'économie de rotor en graphite:
Pour les fonderies en alliage en aluminium et les usines de produits en aluminium, il est important de réduire les coûts de traitement. À cet égard, les rotors de graphite produits par notre entreprise peuvent apporter les avantages suivants:
1. Réduire les coûts de traitement
2. Réduire la consommation de gaz inertes
3. Réduire le contenu en aluminium dans les scories
4. Réduire les coûts de main-d'œuvre
5. Performance, cycle de remplacement plus long
6. Améliorer la fiabilité et réduire les coûts de maintenance.
Conception et commande de rotors en graphite:
En raison des spécifications variables des rotors de graphite utilisés sur chaque ligne de production de moulage ou de roulement. Premièrement, le client fournira les dessins de conception d'origine et un formulaire complet d'enquête sur l'environnement d'utilisation sur site pour le rotor de graphite. Ensuite, sur la base des dessins, une analyse technique sera effectuée en combinant la vitesse, la direction de rotation et la position relative avec le niveau de liquide en aluminium du rotor de graphite, et un plan de traitement anti-érosion approprié sera proposé.
La buse rotative du rotor de graphite est en graphite de haute pureté. In addition to considering the need to disperse bubbles, the structure of the nozzle also utilizes the centrifugal force generated by stirring the aluminum alloy melt to evenly mix the melt into the nozzle with the horizontally sprayed gas, forming a gas/liquid flow to spray out, increasing the contact area and contact time between the bubbles and the aluminum alloy liquid, and improving the degassing and purification effect. La vitesse du rotor de graphite peut être ajustée sans pas grâce à un contrôle de vitesse du convertisseur de fréquence, jusqu'à 700? R / min. La spécification du rotor de graphite est de φ 70 mm ~ 250 mm, avec des spécifications de la roue de φ 85 mm ~ 350 mm, le rotor de graphite de haute pureté a des caractéristiques telles que la haute résistance, la résistance à haute température et la résistance à la corrosion d'écoulement en aluminium. Pendant le processus de purification et de dégazage, l'azote est introduit pour couvrir la surface du liquide en alliage en aluminium à l'intérieur de la boîte pour la protection, en gardant la partie exposée du rotor de graphite dans un gaz inerte pour empêcher l'oxydation à haute température du rotor et prolonger sa durée de vie. La forme de la roue est rationalisée, ce qui peut réduire la résistance pendant la rotation, et la force de frottement et d'érosion générée entre la roue et le liquide en alliage en aluminium est également relativement faible. Il en résulte un taux de dégazage de plus de 50%, du raccourcissement du temps de fusion et de la réduction des coûts de production.
Heure du poste: oct-04-2023