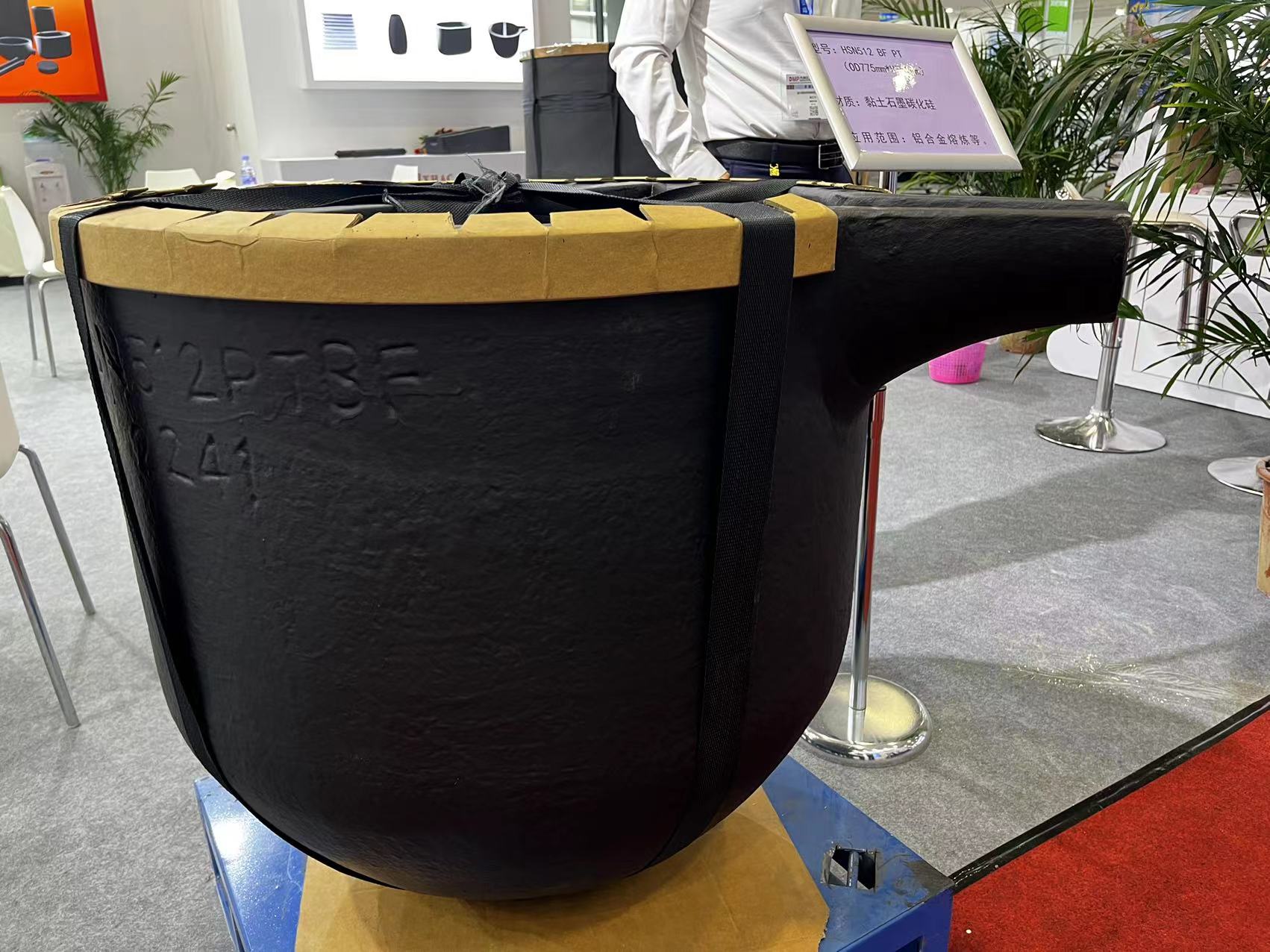
La méthode de préparation de haute résistancecreuset en carbure de silicium et graphitepour la fusion des métaux comprend les étapes suivantes : 1) préparation des matières premières ;2) mélange primaire ;3) séchage du matériau ;4) concassage et criblage ;5) préparation des matériaux secondaires ;6) mélange secondaire ;7) pressage et moulage ;8) coupe et parage ;9) séchage ;10) vitrage ;11) tir primaire ;12) imprégnation ;13) tir secondaire ;14) revêtement ;15) produit fini.Le creuset produit à l'aide de cette nouvelle formule et de ce nouveau processus de production présente une forte résistance aux températures élevées et à la corrosion.La durée de vie moyenne du creuset atteint 7 à 8 mois, avec une structure interne uniforme et sans défaut, une résistance élevée, des parois minces et une bonne conductivité thermique.De plus, la couche de glaçage et le revêtement en surface, ainsi que les multiples processus de séchage et de cuisson, améliorent considérablement la résistance à la corrosion du produit et réduisent la consommation d'énergie d'environ 30 %, avec un degré élevé de vitrification.
Ce procédé concerne le domaine du moulage de la métallurgie non ferreuse, en particulier le procédé de préparation d'un creuset en graphite de carbure de silicium à haute résistance pour la fusion des métaux.
[Technologie de base] les creusets spéciaux en carbure de silicium graphite sont principalement utilisés dans les processus de moulage et de forgeage de métaux non ferreux, ainsi que dans la récupération et le raffinage des métaux précieux, et dans la production de produits à haute température et résistants à la corrosion requis pour les plastiques, fabrication de céramique, de verre, de ciment, de caoutchouc et de produits pharmaceutiques, ainsi que des conteneurs résistants à la corrosion requis dans l'industrie pétrochimique.
Les formulations et les processus de production existants de creusets spéciaux en graphite et en carbure de silicium produisent des produits avec une durée de vie moyenne de 55 jours, ce qui est trop court.Les coûts d'utilisation et de production continuent d'augmenter, et la quantité de déchets générés est également élevée.Par conséquent, la recherche d’un nouveau type de creuset spécial en graphite et en carbure de silicium et de son processus de production constitue un problème urgent à résoudre, car ces creusets ont des applications importantes dans divers domaines chimiques industriels.
Pour résoudre les problèmes ci-dessus, un procédé de préparation de creusets en graphite et en carbure de silicium à haute résistance pour la fusion de métaux est proposé.Les produits préparés selon cette méthode résistent aux températures élevées et à la corrosion, ont une longue durée de vie et permettent de réaliser des économies d'énergie, une réduction des émissions, une protection de l'environnement et un taux de recyclage élevé des déchets pendant la production, maximisant ainsi la circulation et l'utilisation des ressources.
La méthode de préparation de creusets en graphite et carbure de silicium à haute résistance pour la fusion des métaux comprend les étapes suivantes :
- Préparation des matières premières : le carbure de silicium, le graphite, l'argile et le silicium métallique sont placés dans leurs trémies d'ingrédients respectives par grue, et le programme PLC contrôle automatiquement le déchargement et le pesage de chaque matériau en fonction du rapport requis.Des vannes pneumatiques contrôlent le déchargement et au moins deux capteurs de pesée sont installés au bas de chaque trémie d'ingrédients.Après pesée, les matériaux sont placés dans un malaxeur par un chariot mobile automatique.L'ajout initial de carbure de silicium représente 50 % de sa quantité totale.
- Mélange secondaire : Une fois que les matières premières sont mélangées dans le malaxeur, elles sont déchargées dans une trémie tampon et les matériaux contenus dans la trémie tampon sont soulevés vers la trémie de mélange par un élévateur à godets pour le mélange secondaire.Un dispositif d'élimination du fer est placé au niveau de l'orifice de décharge de l'élévateur à godets, et un dispositif d'ajout d'eau est placé au-dessus de la trémie de mélange pour ajouter de l'eau tout en remuant.Le débit d'ajout d'eau est de 10 L/min.
- Séchage du matériau : Le matériau humide après mélange est séché dans un équipement de séchage à une température de 120-150°C pour éliminer l'humidité.Après séchage complet, le matériau est retiré pour un refroidissement naturel.
- Concassage et criblage : Le matériau aggloméré séché entre dans un équipement de concassage et de criblage pour le pré-broyage, puis entre dans un concasseur de contre-attaque pour un concassage ultérieur et passe simultanément à travers un équipement de criblage à 60 mailles.Les particules de plus de 0,25 mm sont renvoyées pour recyclage pour un pré-broyage, un concassage et un criblage ultérieurs, tandis que les particules de moins de 0,25 mm sont envoyées vers une trémie.
- Préparation des matériaux secondaires : Les matériaux présents dans la trémie de décharge sont ramenés à la machine à doser pour une préparation secondaire.Les 50 % restants de carbure de silicium sont ajoutés lors de la préparation secondaire.Les matériaux après la préparation secondaire sont envoyés au malaxeur pour être remélangés.
- Mélange secondaire : pendant le processus de mélange secondaire, une solution spéciale avec une viscosité est ajoutée à la trémie de mélange via un dispositif d'ajout de solution spécial avec une densité spécifique.La solution spéciale est pesée par un seau de pesée et ajoutée à la trémie de mélange.
- Pressage et moulage : Les matériaux après le mélange secondaire sont envoyés vers une trémie de presse isostatique.Après chargement, compactage, aspiration et nettoyage dans le moule, les matériaux sont pressés dans la presse isostatique.
- Coupe et rognage : cela comprend la coupe de la hauteur et la coupe des bavures du creuset.La découpe est effectuée par une machine de découpe pour couper le creuset à la hauteur requise, et les bavures après découpe sont coupées.
- Séchage : Le creuset, après avoir été découpé et paré à l'étape (8), est envoyé dans une étuve pour séchage, avec une température de séchage de 120-150°C.Après séchage, il est maintenu au chaud pendant 1 à 2 heures.L'étuve de séchage est équipée d'un système de réglage des conduits d'air, composé de plusieurs plaques d'aluminium réglables.Ces plaques d'aluminium réglables sont disposées sur les deux côtés intérieurs de l'étuve, avec un conduit d'air entre deux plaques d'aluminium.L'écart entre deux plaques d'aluminium est ajusté pour réguler le conduit d'air.
- Glaçage : Le glaçage est obtenu en mélangeant des matériaux de glaçage avec de l'eau, notamment de la bentonite, de l'argile réfractaire, de la poudre de verre, de la poudre de feldspath et de la carboxyméthylcellulose de sodium.L'émail est appliqué manuellement au pinceau lors du glaçage.
- Cuisson primaire : Le creuset avec glaçure appliquée est cuit une fois dans un four pendant 28 à 30 heures.Pour améliorer l'efficacité de la cuisson, un lit de four labyrinthe avec effet d'étanchéité et blocage de l'air est placé au fond du four.Le lit du four a une couche inférieure de coton d'étanchéité, et au-dessus du coton d'étanchéité, il y a une couche de brique isolante, formant un lit de four labyrinthe.
- Imprégnation : Le creuset cuit est placé dans une cuve d'imprégnation pour une imprégnation sous vide et sous pression.La solution d'imprégnation est transportée vers le réservoir d'imprégnation via une canalisation scellée et le temps d'imprégnation est de 45 à 60 minutes.
- Cuisson secondaire : Le creuset imprégné est placé dans un four pour une cuisson secondaire pendant 2 heures.
- Revêtement : Le creuset après cuisson secondaire est recouvert d'une peinture à base de résine acrylique à base d'eau sur la surface.
- Produit fini : Une fois le revêtement terminé, la surface est séchée et après séchage, le creuset est emballé et stocké.
Heure de publication : 20 mars 2024